Stainless Steel 904L 1.4539
Application
Chemical plant, oil refinery, petrochemical plants, bleaching tanks for the paper industry, combustion gas desulfurisation plants, application in sea water, sulphuric and phosphoric acid. Due to the low C-content, the resistance to intergranular corrosion is also guaranteed in the welded condition.
Chemical Compositions
Element | % Present (in product form) |
Carbon (C) | 0.02 |
Silicon (Si) | 0.70 |
Manganese (Mn) | 2.00 |
Phosphorous (P) | 0.03 |
Sulfur (S) | 0.01 |
Chromium (Cr) | 19.00 - 21.00 |
Nickel (Ni) | 24.00 - 26.00 |
Nitrogen (N) | 0.15 |
Molybdenum (Mo) | 4.00 - 5.00 |
Copper (Cu) | 1.20 - 2.00 |
Iron (Fe) | Balance |
Mechanical properties
Mechanical properties (at room temperature in annealed condition)
Product Form | |||||||
C | H | P | L | L | TW/TS | ||
Thickness (mm) Max. | 8.0 | 13.5 | 75 | 160 | 2502) | 60 | |
Yield Strength | Rp0.2 N/mm2 | 2403) | 2203) | 2203) | 2304) | 2305) | 2306) |
Rp1.0 N/mm2 | 2703) | 2603) | 2603) | 2603) | 2603) | 2503) | |
Tensile Strength | Rm N/mm2 | 530 - 7303) | 530 - 7303) | 520 - 7203) | 530 - 7304) | 530 - 7305) | 520 - 7206) |
Elongation min. in % | Jmin (Longitudinal) | - | 100 | 100 | 100 | - | 120 |
Jmin (Transverse) | - | 60 | 60 | - | 60 | 90 |
Reference data
Density at 20°C kg/m3 | 8.0 | |
Thermal Conductivity W/m K at | 20°C | 12 |
Modulus of Elasticity kN/mm2 at | 20°C | 195 |
200°C | 182 | |
400°C | 166 | |
500°C | 158 | |
Specific Thermal Capacity at 20°C J/kg K | 450 | |
Electrical Resistivity at 20°C Ω mm2/m | 1.0 |
Processing / Welding
Standard welding processes for this steel grade are:
- TIG-Welding
- MAG-Welding Solid Wire
- Arc Welding (E)
- Laser Bean Welding
- Submerged Arc Welding (SAW)
When choosing the filler metal, the corrosion stress has to be regarded, as well. The use of a higher alloyed filler metal can be necessary due to the cast structure of the weld metal. A preheating is not necessary for this steel. A heat treatment after welding is normally not usual. Austenitic steels only have 30% of the thermal conductivity of non-alloyed steels. Their fusion point is lower than that of non-alloyed steel therefore austenitic steels have to be welded with lower heat input than non-alloyed steels. To avoid overheating or burn-through of thinner sheets, higher welding speed has to be applied. Copper back-up plates for faster heat rejection are functional, whereas, to avoid cracks in the solder metal, it is not allowed to surface-fuse the copper back-up plate. This steel has an extensively higher coefficient of thermal expansion as non-alloyed steel. In connection with a worse thermal conductivity, a greater distortion has to be expected. When welding 1.4539 all procedures, which work against this distortion (e.g. back-step sequence welding, welding alternately on opposite sides with double-V butt weld, assignment of two welders when the components are accordingly large) have to be respected notably. For product thicknesses over 12mm the double-V butt weld has to be preferred instead of a single-V butt weld. The included angle should be 60° - 70°, when using MIG-welding about 50° are enough. An accumulation of weld seams should be avoided. Tack welds have to be affixed with relatively shorter distances from each other (significantly shorter than these of non-alloyed steels), in order to prevent strong deformation, shrinking or flaking tack welds. The tacks should be subsequently grinded or at least be free from crater cracks. 1.4539 in connection with austenitic weld metal and too high heat input the addiction to form heat cracks exists. The addiction to heat cracks can be confined, if the weld metal features a lower content of ferrite (delta ferrite). Contents of ferrite up to 10% have a favourable effect and do not affect the corrosion resistance generally. The thinnest layer as possible have to be welded (stringer bead technique) because a higher cooling speed decreases the addiction to hot cracks. A preferably fast cooling has to be aspired while welding as well, to avoid the vulnerability to intergranular corrosion and embrittlement. 1.4539 is very suitable for laser beam welding (weldability A in accordance with DVS bulletin 3203, part 3). With a welding groove width smaller than 0.3mm respectively 0.1mm product thickness the use of filler metals is not necessary. With larger welding grooves a similar filler metal can be used. With avoiding oxidation within the seam surface laser beam welding by applicable backhand welding, e.g. helium as inert gas, the welding seam is as corrosion resistant as the base metal. A hot crack hazard for the welding seam does not exist, when choosing an applicable process. 1.4539 is alos suitable for laser beam fusion cutting with nitrogen or flame cutting with oxygen. The cut edges only have small heat affected zones and are generally free of mirco cracks and thus are well formable. While choosing an applicable processes the fusion cut edges can be converted directly. Especially, they can be welded without any further preparation. While processing only stainless tools like steel brushes, pneumatic picks and so on are allowed, in order to not endanger the passivation. It should be neglected to mark within the welding seam zone with oleaginous bolts or temperature indicating crayons. The high corrosions resistance of this stainless steel is based on the formation of a homogeneous, compact passive layer on the surface. Annealing colours, scales, slag residues, tramp iron, spatters and such like have to be removed, in order to not destroy the passive layer. For cleaning the surface the processes brushing, grinding, pickling or blasting (iron-free silica sand or glass spheres) can be applied. For brushing only stainless steel brushes can be used. Pickling of the previously brushed seam area is carried out by dipping and spraying, however, often pickling pastes or solutions are used. After pickling a carefully flushing with water has to be done.
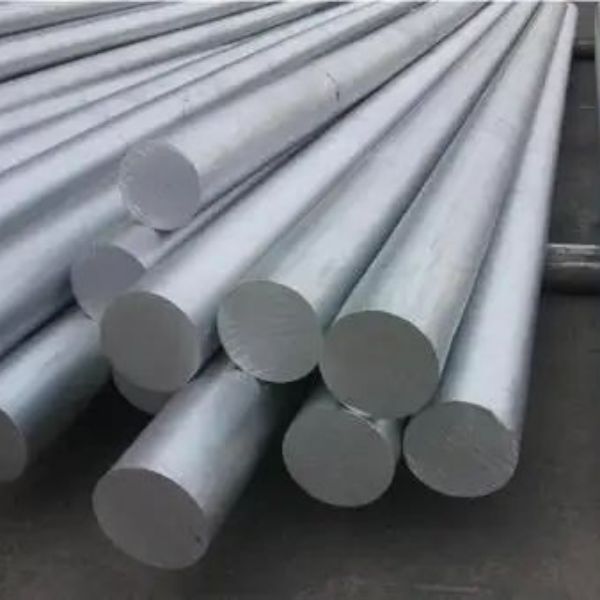
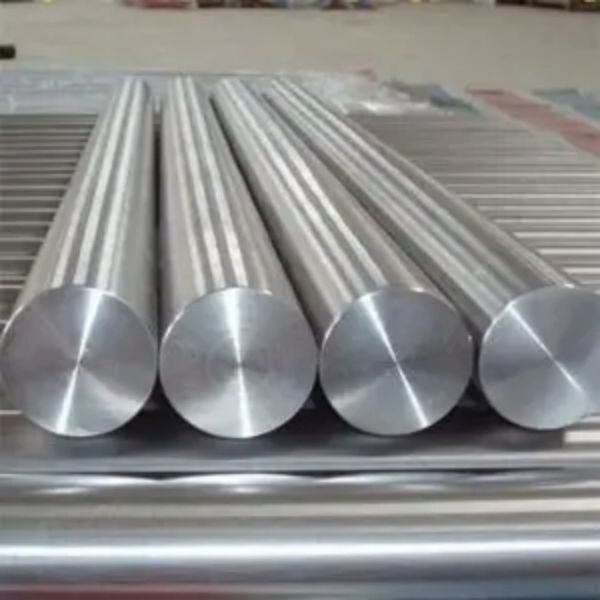
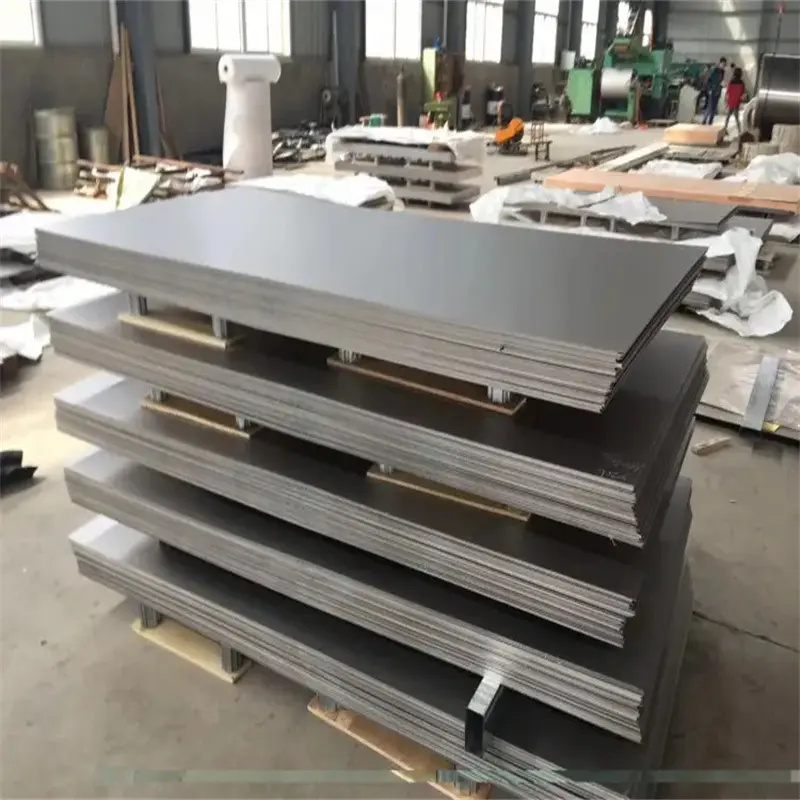
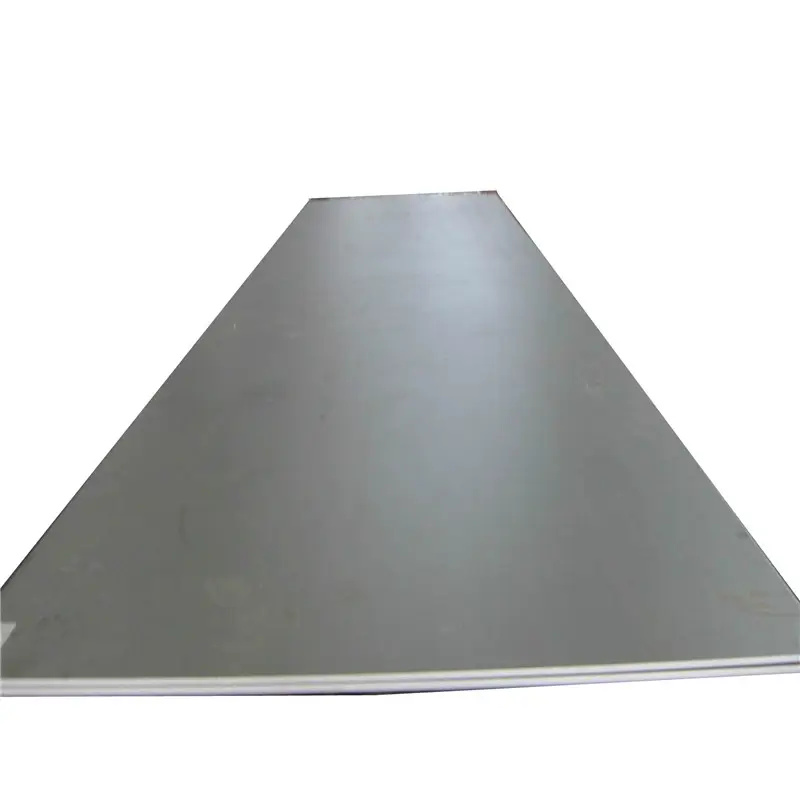